La planta del Grupo BMW en Landshut (Alemania) continúa aumentando su capacidad de producción en lo relativo a los coches eléctricos y ampliará sus instalaciones para dar abasto a los eléctricos Neue Klasse de próxima generación.
Mientras Mercedes-Benz, el máximo rival de BMW, ha levantado el pie del acelerador con sus planes de electrificación, la compañía muniquesa (es decir, BMW) no sólo sigue avanzando sino que acaba de anunciar nuevas inversiones para aumentar la producción de piezas para coches eléctricos en la mayor fábrica de componentes de la compañía.
El Grupo BMW invertirá 200 millones de euros para ampliar las instalaciones donde se fabricará la carcasa de la unidad de propulsión eléctrica (motor más transmisión) de los modelos Neue Klasse, una nueva generación de coches eléctricos que supondrán un importante salto tecnológico para la marca. Con esta inversión, se alcanzan los 1.000 millones de euros canalizados a esta moderna fábrica desde el año 2020.
De ese total, unos 500 millones de euros se han destinado a la ampliación de la planta para cubrir lo relacionado con los coches eléctricos. La capacidad de producción anual de carcasas de aluminio de quinta y sexta generación aumentará alrededor de un 30 por ciento.
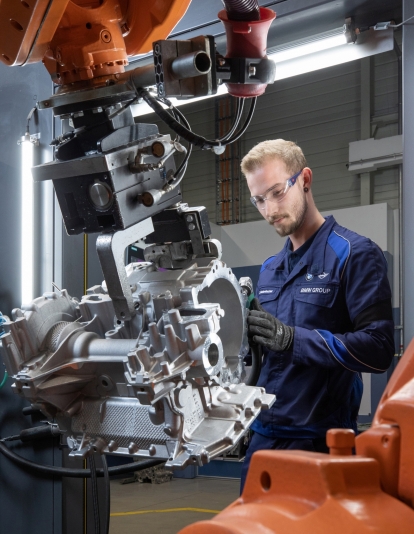
Actualmente se está construyendo una nueva planta de producción que se distribuirá en tres niveles. En el futuro, la fabricación se realizará en dos líneas de producción con una superficie de 12.000 metros cuadrados mediante el proceso de fundición por inyección. Además de garantizar propiedades mecánicas óptimas, este proceso tiene la ventaja adicional de acortar los tiempos de producción y, como resultado, reducir considerablemente el consumo de energía y las emisiones de carbono (debido a la menor temperatura de fundición).
Los planes de expansión no se quedan ahí: en enero de este año, BMW compró unos terrenos de unos 30.000 metros cuadrados adyacentes a la planta Landshut que se destinarán a ampliar la capacidad de producción en el futuro y poder "responder a la demanda futura". Aunque estarán destinados a tecnologías de la movilidad eléctrica, todavía no se ha decidido qué tipo de instalaciones se construirán exactamente en estos nuevos terrenos. El año pasado contrataron a más de 250 nuevos empleados para esta fábrica (la plantilla actual alcanza los 3.700) y se contratarán "cientos de personas más" durante este 2024.
De manera paralela, se está poniendo en marcha un programa de formación para acompañar la transformación gradual de la fábrica hacia la movilidad eléctrica, centrándose en las necesidades tecnológicas futuras en las áreas de robótica, gestión de procesos y calidad, análisis eléctrico y electrónico, mantenimiento y logística. En esa formación se incluye un curso de doce meses en electricidad y electrónica para obtener el título de electricista industrial. Además, también hay en marcha un programa de formación para 17 estudiantes cada año/curso.
Una fábrica de componentes muy importante para BMW
La planta del Grupo BMW en Landshut tiene una relevancia fundamental para la compañía. En 2023, produjo un total de 3,6 millones de piezas de fundición, 430.000 piezas de plástico para exteriores de los vehículos (molduras decorativas y paragolpes), más de 300.000 piezas de CFRP (plástico reforzado con fibra de carbono), 286.000 paneles de instrumentos, 1,4 millones de ejes de transmisión y 20.000 motores "especiales", que suponemos hace referencia a los motores de los modelos BMW M.
En Landshut también se hacen los puestos de conducción de los BMW Serie 5, BMW Serie 6, BMW Serie 7 y BMW iX; los paneles de cuero artificial, cuero, microfibra y tela; componentes estructurales, techos y capós de CFRP; guanteras; parachoques; alerones y otros elementos decorativos.
Además de la importante ampliación de las líneas de producción, BMW también está invirtiendo en mejorar la tecnología de sus moldes de arena en la zona de fundición de metales ligeros. Estos moldes se utilizan en seis tipos diferentes de culatas de motores térmicos. La planta hace diariamente 4.500 unidades con 17 impresoras mediante un proceso de impresión 3D a gran escala. Los núcleos de arena se moldean imprimiéndolos capa por capa en un sistema de cabezal de impresión utilizando aglutinantes inorgánicos libres de emisiones y respetuosos con el medio ambiente.