El cambio radical que está viviendo la industria del automóvil está provocando que los sectores secundarios que alimentan al principal, la venta de vehículos eléctricos, estén experimentando una metamorfosis de la misma magnitud. Si bien algunos de ellos desaparecerán y otros evolucionarán o transformarán sus productos, también aparecerán algunos nuevos que o bien no se existían o bien van a crecer de tal manera que incluso superarán al principal.
Junto a los motores, las baterías son el elemento distintivo de los vehículos eléctricos y las que generan a su alrededor una mayor cantidad de líneas de negocio. A pesar de que la tendencia de la industria es hacia alcanzar una mayor densidad energética, lo que supone una reducción en el uso de materiales, el informe de la consultora IDTechEx indica que este mercado se multiplicará por 12 entre 2021 y 2033.
Toda la información está comprendida en su nuevo informe “Materiales para celdas y paquetes de baterías de vehículos eléctricos 2023-2033". En él se analiza la química de la batería, la densidad de energía y la evolución del diseño para determinar la demanda del mercado para 27 materiales diferentes desde 2021 y hasta 2033. El informe tiene en cuenta coches eléctricos, autobuses, camiones, furgonetas, vehículos de dos y tres ruedas y microcoches.
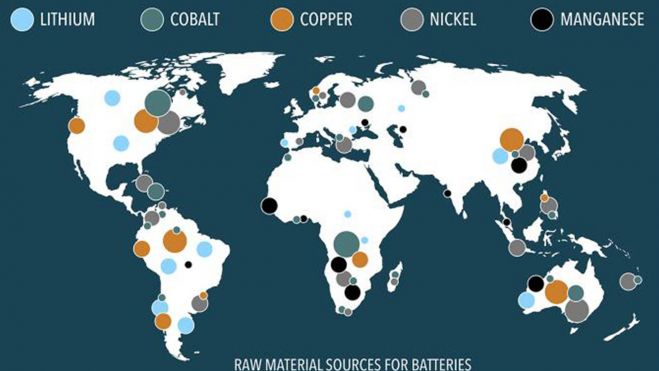
Materiales químicos para las baterías
La química de la batería continúa evolucionando con el objetivo de lograr una mayor densidad de energía. Sin embargo, otros factores, como el coste de la celda y la diversidad de la cadena de suministro, han creado una demanda de productos químicos alternativos fuera de los componentes principales de las baterías más utilizadas, las ternarias con cátodos NMC (níquel, manganeso, cobalto).
En el cátodo, la terna NMC proporciona la densidad de energía más alta. Para mejorarla y evitar el uso de cobalto, se está aumentando el uso de níquel, dando lugar a la fórmula NCM 811 (80% de níquel, 10% de cobalto y 10% manganeso) en comparación con el que incluyen las NCM 111/523 anteriores. El cobalto es un material más costoso, tiene un suministro muy restringido geográficamente y se extrae con prácticas mineras cuestionables. La tendencia a químicas ricas en níquel reduce estos inconvenientes, aunque, por otro lado, aumenta la demanda de este material.
Las baterías que utilizan químicas LFP (fosfato de hierro y litio) fueron prácticamente abandonadas por el mercado de vehículos eléctricos en 2018-2019 debido a que mostraban una menor densidad de energía que las NCM. Sin embargo, la necesidad de una mayor variedad en el suministro de celdas y la capacidad de reducir costes ha provocado su resurgimiento y su adopción especialmente en los niveles de entrada de los vehículos. El impacto en la densidad de energía del uso de LFP se ha visto algo compensado por las mejoras en la eficiencia del empaquetamiento. Esta circunstancia mitiga en parte la demanda de materiales como el níquel y el cobalto.
Además de la química del cátodo, también ha habido innovaciones en la del ánodo. La incorporación de pequeños porcentajes de silicio que mejora la densidad de energía, da como resultado la reducción de la necesidad de grafito, el material con el que habitualmente se fabrica la microestructura de este electrodo. En el futuro, las baterías con ánodo predominantes en silicio serán habituales.
También hay otros materiales críticos para el funcionamiento de una celda de batería, como las láminas colectoras o los aglutinantes. IDTechEx predice que la demanda aumentará anualmente en una proporción de 9,4 veces, a pesar del aumento generalizado de la densidad energética de las baterías.
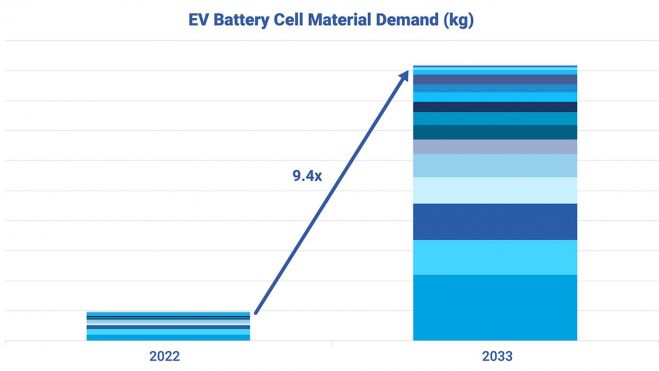
Materiales para el empaquetamiento de las baterías
Si bien es importante aumentar la densidad de energía modificando la composición química de sus celdas, también es crucial la manera en la que se construye el paquete en su conjunto. Reducir las zonas vacías y los elementos accesorios aumenta el espacio disponible para el material activo lo que también tiene repercusión sobre la densidad.
El mercado ha reducido gradualmente la cantidad de materiales utilizados para empaquetar las celdas, aumentando la relación entre el peso y el volumen del paquete. El cambio radical en este sentido es la adopción de diseños de celda a paquete eliminando los módulos intermedios con los que se agrupaban las celdas. A pesar de la reducción de materiales que esto provoca, el crecimiento del mercado de vehículos eléctricos implica una mayor demanda de los materiales de empaquetamiento.
La gestión térmica es crucial para mantener las celdas a una temperatura de funcionamiento óptima. Requiere componentes como placas frías y mangueras de refrigerante, materiales de interfaz térmica que ayudan en la transferencia de calor entre las celdas y la estructura de enfriamiento.
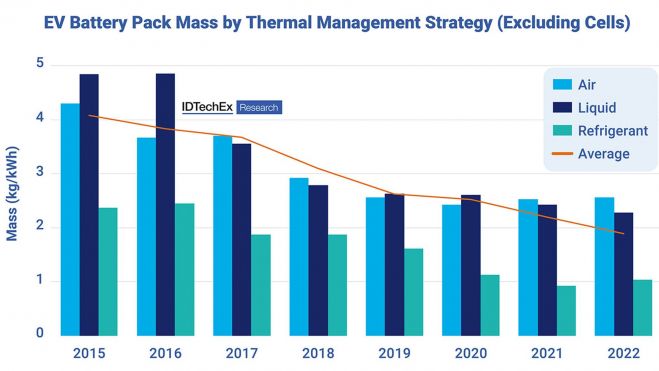
Además, para evitar que una fuga térmica se propague entre las celdas y también hacia fuera del paquete de baterías, se requieren materiales de protección pasiva contra incendios. La forma en que estos materiales y componentes de gestión térmica se integran se está simplificando, especialmente con la adopción de diseños de celda a paquete, pero seguirán siendo componentes operativos críticos con una mayor demanda.
Para ahorrar peso en las carcasas de las baterías, que se fabrican con aluminio y acero, se emplean compuestos y polímeros además del uso de blindajes EMI para el sistema de protección contra incendios.
El informe de IDTechEx hace un pronóstico sobre los materiales utilizados en celdas y paquetes: aluminio, acero, cobre, litio, cobalto, níquel, manganeso, electrolito, hierro, fósforo, aglutinantes, carcasas, negro de humo, silicio, separadores, nanotubos de carbono, polímero reforzado con fibra de carbono, polímero reforzado con fibra de vidrio, materiales de interfaz térmica, materiales de protección contra incendios, aislamiento eléctrico, placas frías y mangueras de refrigeración.