Tesla está cambiando para siempre la historia del automóvil. Dentro de unos años, los libros relatarán lo que ahora estamos viendo pasar como espectadores. No solo es la irrupción de la propulsión eléctrica que trae consigo múltiples consecuencias relacionadas con la movilidad. Tesla ha cambiado la industria haciendo que entren a formar parte de ella actores que antes estaban fuera y, probablemente, provocando que marcas históricas acaben desapareciendo. La última revolución de los californianos está pasando ahora: se trata de la manera de construir los coches.
En los últimos años, los americanos han estado invirtiendo mucho dinero y mucho tiempo en tecnologías de fundición para acelerar el proceso de fabricación de sus coches eléctricos. Sus programas de I+D se han basado en el desarrollo de nuevas aleaciones que permitan conformar piezas fundidas más grandes, lo que simplifica enormemente el proceso de ensamblaje.
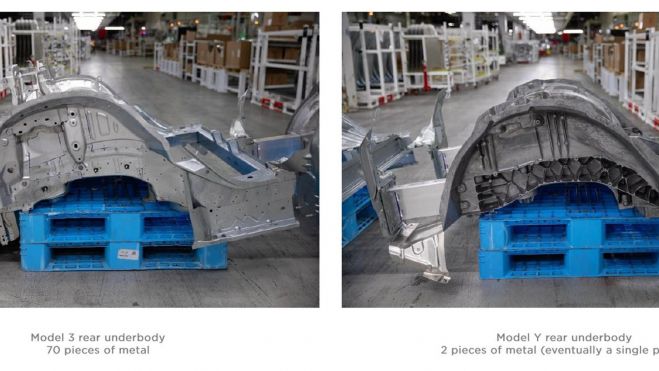
Con esto, el fabricante ha logrado, reducir el número de piezas que se necesitan para crear el chasis del Model Y (que es con el que ha iniciado estos procedimientos). El subchasis delantero y el trasero se fresan a partir de la fundición de una sola pieza. Además, cómo las piezas grandes de aluminio se deforman cuando se tratan térmicamente, Tesla ha desarrollado su propia aleación, capaz de lograr niveles altísimos de resistencia y durabilidad, ahorrando costes de material y también de energía, ya que no se requieren grandes hornos de curado. Además, al ir toda esa parte unida, no es necesario mecanizarla.
Lo que no gusta en Japón
Varios de los fabricantes más importantes del mundo ya han mostrado interés por esta nueva manera de ensamblar coches eléctricos. Las máquinas de fundición a presión de gran tamaño son capaces de producir piezas de aluminio mucho más grandes que cualquier otra que se haya usado antes en la fabricación de automóviles.
Toyota, el fabricante más importante de Japón, ya ha reconocido la bondad del proceso ideado por Tesla y ha anunciado que lo utilizará. La nueva unidad BEV Factory Bussines, encargada de diseñar la nueva plataforma para vehículos eléctricos, implementará estos sistemas. Para poner en contexto sus ventajas, actualmente la sección inferior trasera del Toyota bZ4X está compuesta por 86 piezas fabricadas mediante 33 procesos, lo que podría reducirse a dos procesos y dos piezas.
Sin embargo empiezan a surgir voces discordantes. JFE Holdings Inc. es la segunda siderúrgica más grande de Japón. Considera que el uso de la tecnología gigacasting representa un riesgo para el negocio de la compañía. "La cantidad de acero crudo utilizado obviamente disminuirá", aseguró su presidente, Koji Kakigi en una conferencia de prensa, calificando todo esto como "un problema muy grande". Dado que el aluminio es menos resistente que el acero, es posible que se necesite utilizar hierro en las partes más vulnerables de los vehículos eléctricos para aumentar la seguridad, añadió.
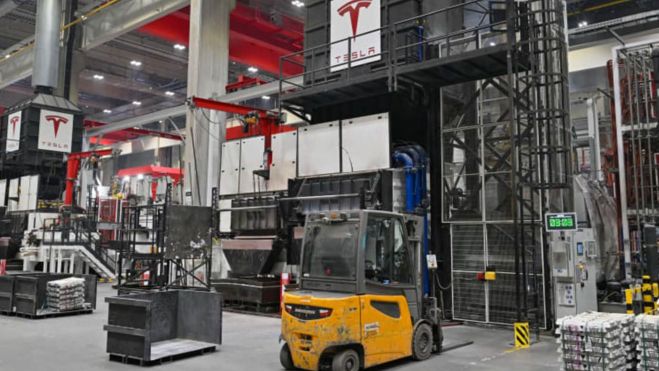
El cambio de paradigma que suponen estos procedimientos representa la rotura de la estrategia a largo plazo de esta empresa japonesa, que no será la única afectada. JFE Holdings está considerando invertir en carbón coquizable, esencial para la fabricación de acero, agregó Kakigi. Pero, para tomar esta decisión, necesita que la demanda se mantenga sólida en las próximas dos décadas.
Además, en mayo, JFE Holdings anunciaba que esperaba incrementar sus beneficios anuales netos en un 17%, hasta los 190.000 millones de yenes (1.250 millones de euros), contando con una mayor demanda de acero provocada por la recuperación del sector del automóvil.