Los vehículos eléctricos no solo implican cambios en las costumbres y en la manera de desplazarnos. Los propietarios tienen que acostumbrarse a recargar sus vehículos y a ser eficientes en la conducción. Y, desgraciadamente, también a pagar más por los vehículos. Pero, para los fabricantes también están cambiando las cosas. Los coches eléctricos no se fabrican igual que los de combustión, requieren otros procedimientos y, algunos, son todavía complicados. Uno de ellos ha supuesto un auténtico cuello de botella, incluso para el ‘más listo de la clase’, Tesla.
Producir los electrodos de la batería y ensamblar los diferentes componentes representa aproximadamente el 24% del coste total de una celda de batería. En los últimos años, los fabricantes han comenzado a investigar procesos alternativos, entre los que destaca el empleo de la tecnología de recubrimiento de electrodos en seco con la que se puede optimizar el proceso.
Este procedimiento se refiere a una técnica utilizada en la fabricación de electrodos para soldadura. A diferencia del proceso de recubrimiento húmedo, el tradicional, en que los electrodos se sumergen en un baño de recubrimiento líquido, con este se aplica el recubrimiento de manera seca directamente sobre el electrodo.
¿Qué tiene Volkswagen que no posee Tesla?
Volkswagen y el fabricante de máquinas de impresión Koenig & Bauer AG aseguran que son las primeras en perfeccionar el procedimiento tanto para el electrodo positivo como para el negativo. Por este camino, el fabricante podría reducir el coste de producción de celdas lo que supone cientos de millones de euros al año, según ha asegurado Thomas Schmall, consejero delegado de la División de Componentes de Volkswagen: "Nadie más puede hacer esto hoy”, ha añadido.
En el procedimiento tradicional para fabricar baterías, a los materiales del cátodo (electrodo positivo) y del ánodo (electrodo negativo) se les aplica una lámina portadora mediante una mezcla de pasta química que necesita secarse, lo que requiere grandes cantidades de energía. El revestimiento en seco elimina ese paso con un adhesivo que no precisa secado, explica Schmall.
Tesla adquirió los conocimientos necesarios para ejecutar este proceso cuando en 2019 compró Maxwell Technologies, una empresa de San Diego que fabrica ultracondensadores.
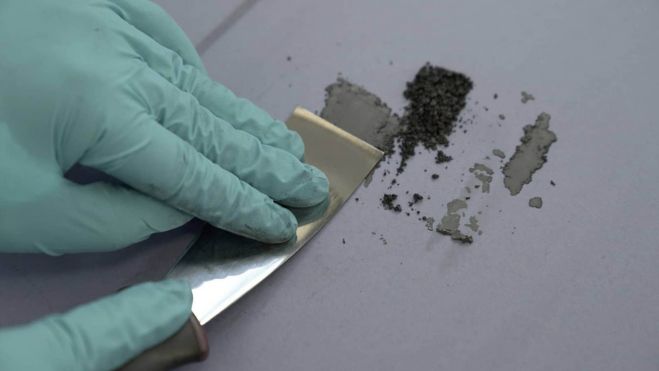
El procedimiento: ventajas e inconvenientes
Con este sistema, una vez aplicado el recubrimiento, los electrodos se someten a un proceso de calentamiento en hornos especiales para fundir y fusionar los ingredientes del recubrimiento. De esta forma, los diferentes componentes reaccionan entre sí y forman la escoria protectora y otros productos químicos necesarios para el proceso de soldadura.
En consecuencia, se obtienen varias ventajas sobre el recubrimiento húmedo convencional.
Mejora del rendimiento, ya que precisan un revestimiento más preciso y uniforme de los electrodos, lo que da como resultado una mayor densidad de energía, una mayor autonomía y tiempos de recarga más rápidos.
Una mejora de la seguridad al reducir el riesgo de cortocircuito y otros peligros, al ser menos propensos a fugas o sobrecalentamiento.
También aumenta la escalabilidad con un enorme potencial para la producción de baterías a gran escala.
Respeta, además, el medioambiente al eliminar la necesidad de solventes y otros productos químicos utilizados en los métodos tradicionales y el proceso de suspensión.
A eso hay que añadir la reducción del consumo de energía durante la fabricación, lo que se traduce en una reducción de costes tanto en materiales de producción como en necesidades de mano de obra y una mayor vida útil reduciendo la necesidad de reemplazos y los costes de propiedad.
Dadas estas ventajas, la tecnología de recubrimiento de electrodo seco es una tecnología valiosa para la industria de vehículos eléctricos. Es escalable y puede adaptarse a la química actual de las baterías de iones de litio e, incluso, tener un uso potencial para las baterías de estado sólido.
Sin embargo, existen algunos retos asociados entre los que se incluyen la necesidad de utilizar equipos especiales para la pulverización del polvo de recubrimiento, el control preciso de las temperaturas de fusión durante el proceso de calentamiento y la necesidad de garantizar una cobertura uniforme del recubrimiento en toda la superficie del electrodo.
Lo que han conseguido los alemanes
Volkswagen asegura que, gracias a esta colaboración con Koenig & Bauer, ha desarrollado un procedimiento con el que ya ha producido varios cientos de celdas en una línea piloto que debería permitir la producción industrial en 2027. Además de la producción a mayor escala con materias primas más baratas, Schmall asegura que esperan alcanzar una reducción de costes de hasta un 50% con respecto a las celdas actuales.
Sus plantas de baterías de Alemania, España y Canadá mantendrán todavía las líneas de secado para el procedimiento tradicional, pero podrán ser eliminadas en una fecha posterior, liberando alrededor del 15% del espacio de la planta, explicó el director de Operaciones de PowerCo, Sebastian Wolf.