Bajo el nombre de Innovation Hub, Volkswagen ha creado una serie de centros de investigación y desarrollo que tienen como objetivo promover la colaboración con startups, universidades, centros de investigación y otras empresas tecnológicas para crear soluciones innovadoras en el campo de la movilidad y la conducción del futuro.
El de Estados Unidos se inauguró en 2020 en el Parque de Investigación de la Universidad de Tennessee (UT), en Cherokee Farm, en Knoxville. Una de las razones por las que se eligió esta ubicación es porque el Laboratorio Nacional de Oakridge (ORNL), financiado con fondos federales, también está allí. Esto facilita que Volkswagen colabore con científicos de UT y ORNL en su investigación sobre vehículos eléctricos. El resultado de su trabajo en estos casi tres años son cuatro innovaciones que pueden ser clave para los futuros coches eléctricos del grupo alemán.
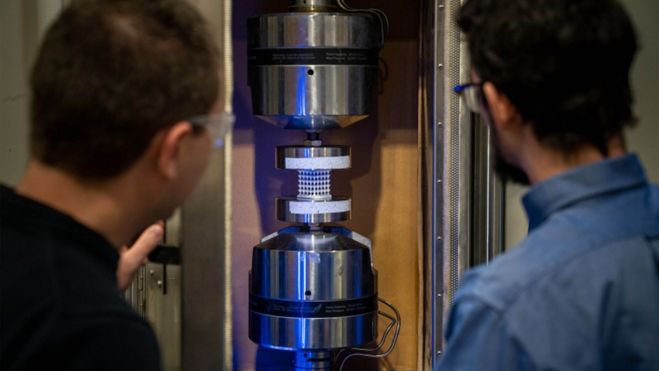
Inteligencia artificial para las nuevas carcasas de las baterías
El equipo de investigadores de Volkswagen trabaja en nuevas estructuras de materiales para reducir el peso de los vehículos, clave para aumentar la eficiencia y, finalmente, la autonomía de los vehículos eléctricos. El objetivo de este primer proyecto piloto es reemplazar el marco de acero que alberga el paquete de baterías de un coche eléctrico por algo más liviano.
Para lograr el mejor material y la mejor forma estructural, recurrió al empleo de inteligencia artificial (IA). Millones de parámetros y combinaciones han alimentado al clúster de computadoras de alto rendimiento de UT. El objetivo era desarrollar una estructura modular repetitiva en forma de pequeñas pirámides que se pudiera imprimir en 3D a partir de resinas líquidas. Su arquitectura está diseñada para que pueda soportar 30.000 veces su propio peso, que es de tan solo 68 gramos.
El marco formado por estas estructuras sería hasta un 60% más liviano que el de acero. Los investigadores descubrieron que, además, es capaz de absorber más energía y actualmente se encuentran comprobando su durabilidad a largo plazo.
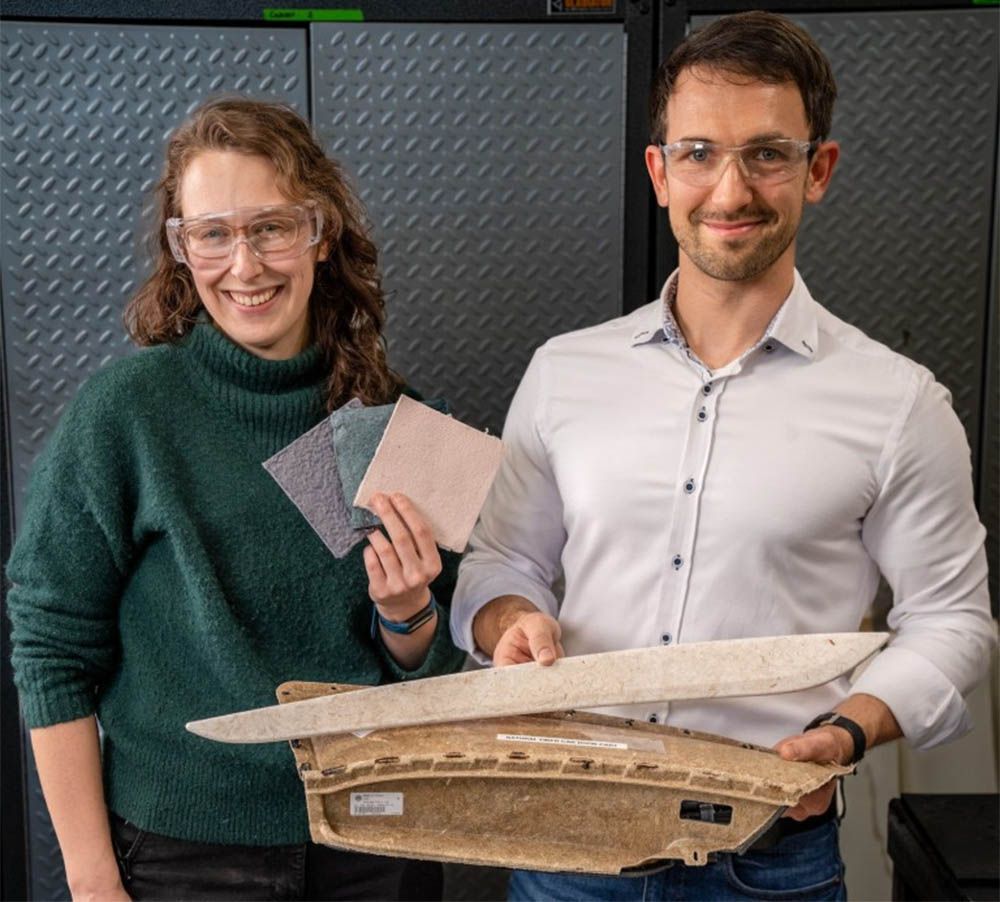
Interiores de los vehículos eléctricos de papel
Los científicos del Centro de Carbono Renovable de la UT están utilizando papel como una alternativa reciclable a las piezas y láminas de plástico que se emplean en los interiores de los vehículos eléctricos. El equipo ha patentado un método de preformado y prensado en caliente de termoplásticos reforzados con fibra de celulosa para hacer que las piezas interiores sean duraderas.
Los compuestos a base de papel reciclable se pueden transformar para crear con ellos varias formas y tamaños interiores. Además, permiten agregar diferentes texturas y colores. Volkswagen se encuentra actualmente en la fase de “verificación” para poder crear parte de los guarnecidos y las piezas de acabado del interior de sus habitáculos de sus vehículos eléctricos futuros a base papel y trabaja para apoyar su producción a escala industrial.
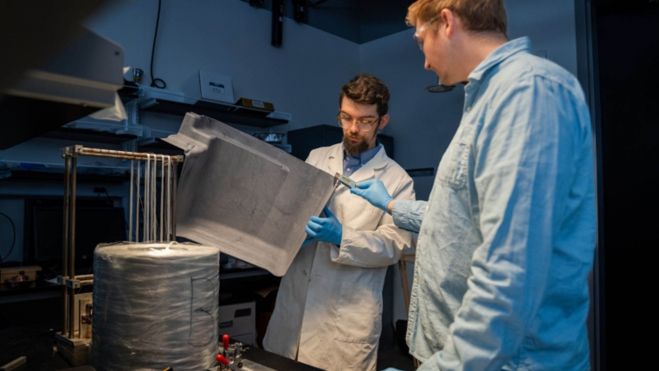
Fibra ligera para la carrocería
Los investigadores recrearon la puerta levadiza de un Volkswagen Atlas 2020 utilizando un compuesto de moldeo en láminas, un tipo de plástico reforzado con fibra de vidrio. La nueva puerta trasera era seis kilogramos más ligera que la de metal, es decir, un 35% menos de peso. Una solución de este tipo puede ser clave de nuevo para aumentar la eficiencia energética, ya que se precisará menos energía para mover menos peso, lo que aumentará la autonomía de los vehículos eléctricos.
Que el material del que están hechas las piezas de la carrocería sea metal o fibra no modifica los procedimientos de ensamblaje, por lo que no afecta a la producción en volumen de los vehículos. Recientemente, los investigadores han refinado aún más los procesos de moldeo y las formas de optimizar la durabilidad, la calidad y las posibilidades de diseño.
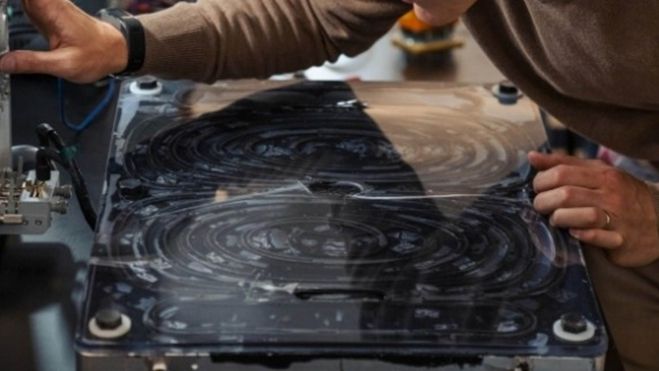
Carga rápida e inalámbrica
Esta es una de las grandes y más prometedoras tecnologías que pueden revolucionar los vehículos eléctricos. Varias son las investigaciones y las pruebas que se están haciendo con estos sistemas para alcanzar tasas de transmisión de energía tan elevadas como las que se logran con los puntos de recarga ultrarrápidos.
El equipo de Volkswagen ha patentado un diseño de bobina y almohadilla de carga con materiales de carburo de silicio. En las primeras pruebas, el fabricante asegura que el prototipo del sistema inversor de carburo de silicio ha demostrado ser muy eficiente. El equipo ha podido aumentar el nivel de potencia de carga alcanzando hasta 120 kW con un prototipo derivado de trabajos anteriores y que tan solo alcanzaba los 6 kW. El objetivo es poder alcanzar potencias de recarga de hasta 300 kW.