Lento, pero seguro. En Japón trabajan con otra filosofía diferente a Occidente y Toyota es uno de los máximos exponentes de esta forma de ver el mundo. La industria del automóvil está patas arriba y, aunque el fabricante japonés parece ver pasar la tormenta sin inmutarse, en la trastienda trabajan para no mojarse.
Con esta estrategia, las baterías evolucionarán durante esta década, pasando por diferentes tecnologías hasta llegar a las de electrolito sólido. Estos paquetes de baterías darán lugar a una nueva línea de vehículos eléctricos de próxima generación que ya se están desarrollando a partir de una hoja en blanco por la recientemente creada división BEV Factory.
Estos modelos dispondrán de nuevas plataformas y sistemas de software y se ensamblarán mediante nuevos métodos de producción. Todos estos avances comprenden lo que su CEO, Koji Sato, llama el Step 3 (‘Paso 3’) del plan de lanzamiento de vehículos eléctricos de Toyota.
El jefe de Tecnología de la marca, Hiroki Nakajima, estima que alrededor de 1,7 de los 3,5 millones vehículos eléctricos vendidos por la empresa en 2030 contarán con todos los avances tecnológicos desgranados en el Step 3.
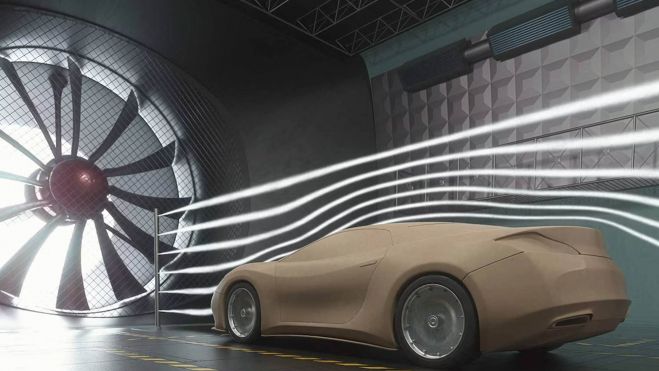
La aerodinámica: aprendiendo del espacio
En el evento Toyota Technical Workshop organizado por la marca en el Centro Técnico Higashi-Fuji, Toyota presentó el concept de un Lexus eléctrico que estará presente en el Japan Mobility Show de este otoño. Su aerodinámica adelanta el nuevo lenguaje de diseño de Toyota, fundamental para exprimir cada kWh de las nuevas baterías.
Bajo la dirección del jefe de Diseño Global, Simon Humphries, su equipo está aprovechando las enseñanzas de los ingenieros de cohetes de la división aeroespacial de Mitsubishi Heavy Industries para mejorar el flujo de aire alrededor de los vehículos. Los diseñadores planean adoptar una tecnología que se utiliza para proteger los cohetes que viajan a velocidades de Mach 30 (37.000 km/h). La técnica crea una película de aire alrededor de la superficie del vehículo que ayuda a reducir la resistencia al viento.
Los coeficientes de arrastre por debajo de 0,20 son el santo grial para los diseñadores. En dos o tres años, Toyota quiere aprovechar este aprendizaje para lograr coeficientes de resistencia aerodinámica de 0,1x en sus automóviles. Cuanto más baja es esta cifra, más resbaladizo es el coche en el aire que le rodea.
Para poner esta cifra en contexto, Hyundai, por ejemplo, peleó por lograr rebajarla en el IONIQ 6, para el que prometía lograr el tan ansiado 0,1x, aunque finalmente tuvo que conformarse con el 0,21. El nuevo Toyota Prius ronda los 0,24, mientras que el Tesla Model 3 obtiene 0,23.
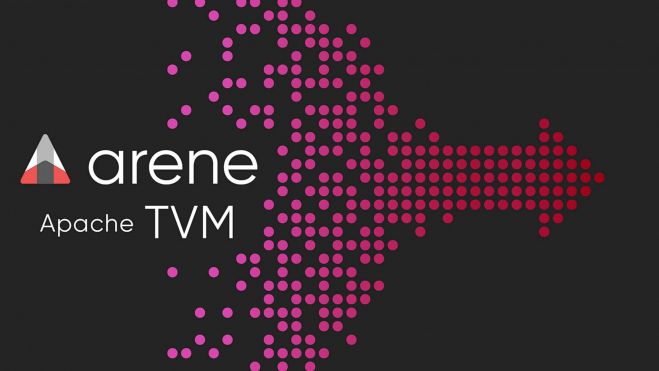
El software reduce el tiempo de desarrollo
Los coches eléctricos del Paso 3 de Toyota incorporarán el sistema operativo Arene que está siendo desarrollado actualmente por su empresa subsidiaria Woven by Toyota, anteriormente conocida como Woven Planet. Si bien el nuevo software incluye aplicaciones especiales para los vehículos 100% eléctricos, en una fase de transición, también se implementará para otro tipo de tecnologías de propulsión.
Mediante actualizaciones inalámbricas automáticas, el cliente dispondrá siempre de la mejor versión existente para su vehículo. Además, Nakajima asegura que el uso de Arene acelerará el desarrollo de los productos.
Takahiro Ishijima, presidente del Centro de Desarrollo de Vehículos de Toyota, añade que la compañía quiere reducir el tiempo de desarrollo inicial de 30 meses hasta 20 con el objetivo de que pueda estar listo en 2026. Actualmente, “Toyota carece de la flexibilidad necesaria para cambiar rápidamente de dirección en medio de ese ciclo de desarrollo y adaptarse a las nuevas tecnologías cuando surjan”, asegura. “Esto es lo que aprendimos de los chinos”, añade.
Takero Kato, presidente de BEV Factory, fue el jefe de Ingeniería de Toyota en la empresa conjunta que crearon con BYD, uno de los principales fabricantes de vehículos eléctricos del mundo, junto a Tesla. Kato aportará a la empresa buena parte de la experiencia que ha supuesto el lanzamiento del bZ3 en China, que fue desarrollado y comercializado en dos tercios del tiempo que habitualmente se dedica a la creación de un nuevo modelo.
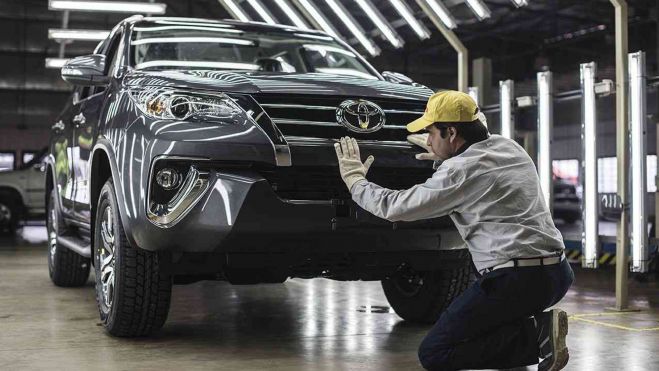
Un sistema de producción completamente renovado
Lograr una producción de vehículos eléctricos eficiente y con un coste lo más bajo posible es crucial para el plan de Toyota. Con ese fin, Toyota también está revisando el famoso Sistema de Producción Toyota (TPS, por sus siglas en inglés-Toyota Production System), que se ha convertido en un referente en la industria y en otros sectores. El TPS se basa en el principio fundamental de eliminar el desperdicio en todas las formas posibles para lograr una producción eficiente y de alta calidad.
Los ingenieros de producción están repensando el sistema desde cero con el objetivo de presentar una serie de nuevas técnicas de fabricación para los vehículos eléctricos de 2026. Su objetivo es reducir a la mitad la cantidad de procesos de producción y la inversión necesaria en la planta.
Las nuevas técnicas incluirán el uso del llamado ‘gigacasting’, un procedimiento para reducir la enorme cantidad de piezas y soportes necesarios de la parte delantera y trasera del vehículo, reduciéndolo a dos módulos de grandes dimensiones. Un sistema que Tesla ya ha comenzado a aplicar en sus plantas de producción.
Actualmente, la sección inferior trasera del Toyota bZ4X está compuesta por 86 piezas fabricadas mediante 33 procesos. Toyota está creando un prototipo de una forma de estampar el mismo módulo como una sola pieza y a partir de un solo proceso, gracias al uso de una gigaprensa. Este procedimiento es “abrumadoramente más rápido", explica a Automotive News Yoshio Nakamura, subdirector de Producción Global, y nos permite “un alto nivel de libertad".
Estas fundiciones se implementarán en las plantas que fabrican vehículos eléctricos Step 3 a partir de 2026. Estarán compuestos esencialmente por tres módulos simplificados, una batería delantera, trasera y central. Esta arquitectura mejorará la eficiencia de fabricación en un 20%. “Eso significa que, con la misma cantidad de materiales y procesos, Toyota podrá fabricar un 20% más de vehículos”, aclara Nakamura.
Toyota también eliminará las líneas de producción ancladas. La idea aquí es que los vehículos se muevan por sí mismos a través de la planta. La marca llama a este sistema producción autopropulsada. Una solución que ya se está utilizando en la planta de ensamblaje Motomachi donde el bZ4X se conduce solo desde el ensamblaje hasta la inspección final.
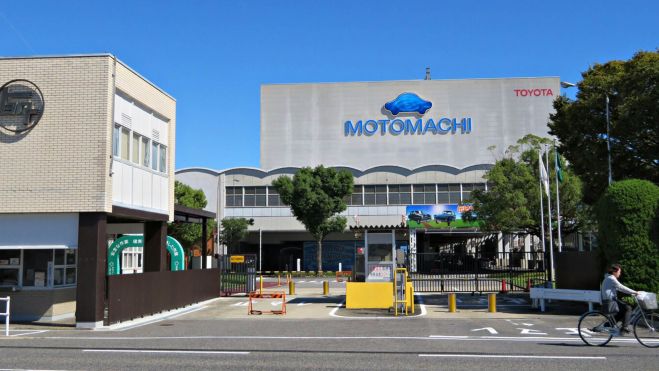
Los ingenieros quieren extender este sistema de conducción autónoma a todo el ensamblaje. El automóvil se desplazará automáticamente hasta las piezas, en lugar de llevar las piezas al automóvil. Este sistema debería reducir drásticamente la inversión en las plantas, puesto que no serán necesarios los transportadores fijos o colgadores que se encargan de arrastrar los automóviles a través de la fábrica.
Otra ventaja de esta forma de trabajar es que permitirá diseño de plantas más compactas y almacenes de piezas más flexibles. Según Nakamura, así se podrán ahorrar cientos de millones de dólares en inversión, reduciendo el tiempo de producción a la mitad. Para mover los vehículos, el sistema utiliza una tecnología de control remoto, similar a la de un automóvil de radiocontrol. En este caso, al ser vehículos eléctricos, pueden moverse con la energía de su propia batería.
Nakamura explica que estos nuevos procedimientos son una extensión, una mejora, del TPS no un nuevo sistema que sustituye al que hasta ahora es el estándar para la fabricación en serie y que se aplica a muchos procesos industriales, desde bancos de alimentos hasta laboratorios de hospitales. “El concepto que hay detrás del Sistema de Producción de Toyota sigue siendo el mismo", asegura Nakamura: “eliminar el desperdicio y el trabajo innecesario".