Visitar una fábrica de coches es siempre interesante, especialmente si tienes cierta curiosidad sobre procesos de industrialización y producción en serie. Miles de detalles tienen que encajar en perfecta armonía para que todo funcione como debe funcionar, y de hecho lo hace. La fábrica de Renault en Valladolid es una de las más importantes de nuestro país, una planta donde se fabrican dos modelos de vital importancia para la marca como son Captur y Symbioz. Y la hemos recorrido de principio a fin.
Con el Plan Industrial Renaulution en España 2020-2024, la compañía francesa adjudicó cinco nuevos vehículos híbridos a España. Los tres más grandes fueron para Palencia (Austral, Espace y Rafale) y los otros dos, para Valladolid.
El Captur es un viejo conocido, un superventas para la marca del rombo, que se ha renovado recientemente. El nuevo Symbioz marca un nuevo hito para la planta vallisoletana, pues es la primera vez en la historia que Valladolid fabrica un coche del segmento C. El año pasado la producción aumentó un 18% respecto al año anterior y se prevé que en 2024 vuelvan a superarse las cifras del año anterior.
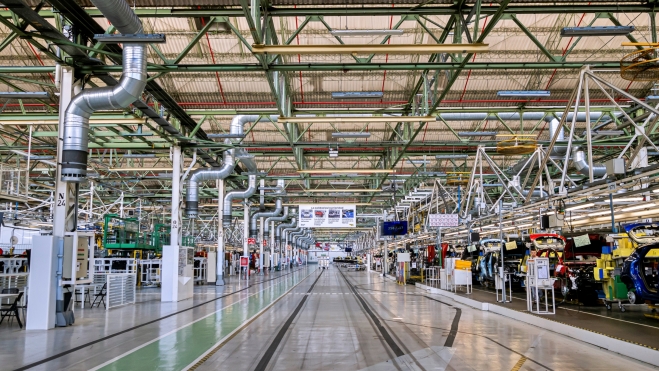
La producción comienza en la Factoría de Carrocerías, con los procesos de fabricación de las piezas que componen el esqueleto del vehículo y que pueden ser metálicas (acero) o plásticas. Aquí se fabrican un total de 137 piezas, desde lo que llaman caja (la estructura principal del vehículo) hasta los paragolpes delanteros y traseros, las puertas, lados de caja, techos, maleteros, traviesas... Para ello existen un total de 13 líneas de producción diferentes.
A esta parte de la fábrica llegan enormes bobinas de acero de 32 toneladas, que se transforman en piezas planas que posteriormente son conformadas en las líneas de embutición altamente automatizadas. Después, en las instalaciones de corte láser se recortan o taladran, según los requisitos de cada pieza.
El taller de chapa, donde la fabricación se automatiza casi al 100%
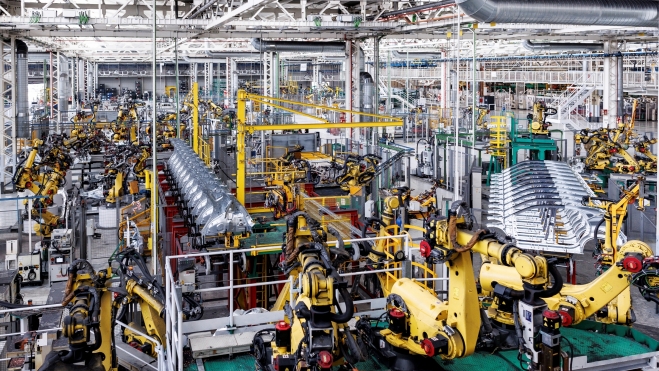
El siguiente paso es el taller de chapa, una parte de la fábrica que está automatizada al 99 por ciento. Aquí hay un total de 770 robots que consiguen hacer 62 coches por hora (más de 1 coche por minuto). Cuando se inauguró la fábrica en 1953, se hacían 10 unidades al día del Renault 4/4. Pese al altísimo nivel de automatización de esta parte de la línea de producción, siguen siendo necesarias un total de 350 personas.
El primer paso en el taller de chapa es la soldadura, donde 50 robots unen mediante diferentes tecnologías (láser y ArPlas) las piezas necesarias para completar una carrocería. En esta parte hay dos tipos de robots: los de manutención, que se encargan de coger y colocar las piezas en el sitio correcto, y los robots de soldadura, cuyo nombre deja claro el trabajo que realizan.
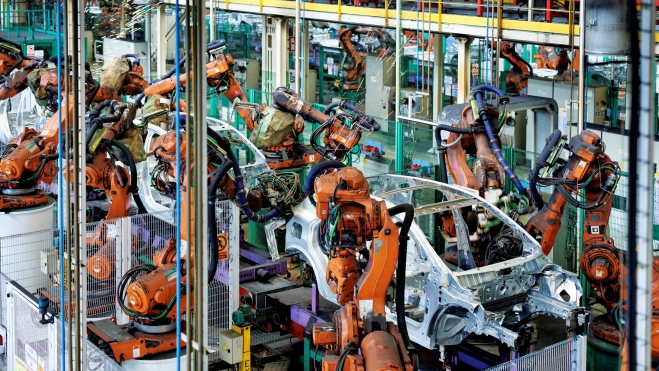
Cada vehículo lleva más de 3.500 puntos de soldadura, de los cuales el 78,8% se realizarán en este punto. Es hipnótico ver cómo los robots colocan los laterales a la caja y después, casi sin saltar chispas, todo queda perfectamente unido.
Control de calidad premium
Después, el vehículo se dirige a la línea de ferraje, donde se colocan las piezas móviles de la carrocería: puertas, capó y maletero. Varias cámaras 3D escanean la carrocería y comprueban que la soldadura láser del techo quede perfecta y los márgenes de ajuste sean conformes a los requisitos del fabricante.
Otras cámaras con inteligencia artificial vuelven a verificar el nivel de calidad. Si detectan un posible fallo de calidad, se alerta a un operario para que vaya a revisarlo. El humano determina en última instancia si efectivamente se trata de un fallo de calidad o si ha sido un error de la cámara. La inteligencia artificial sirve para que la cámara aprenda de sus errores y sea cada vez más precisa en la detección.
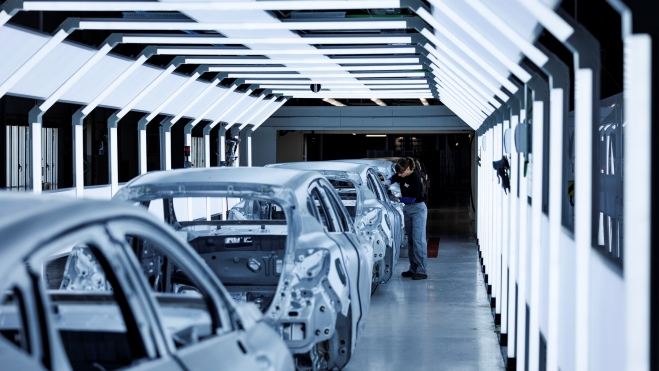
Por último, antes de enviar la carrocería al taller de pintura, se realiza un control de aspecto y calidad en el "túnel de calidad premium" (así lo llama Renault), donde se busca cualquier mínimo fallo de calidad.
Taller de pintura, uno de los procesos más exigentes e interesantes
Cuando visitamos la fábrica, los anfitriones de Renault priorizaban nuestra seguridad en todo momento y, como es lógico, no podíamos acariciar los robots. Sin embargo, estaban cerca al otro lado de las protecciones. En el taller de pintura, la cosa cambia un poco. Se parece más a un laboratorio y las condiciones de limpieza tienen que ser prácticamente obsesivas, así que vemos casi todo a través de cristales y cabinas que aíslan los coches del exterior (incluidas las visitas como nosotros).
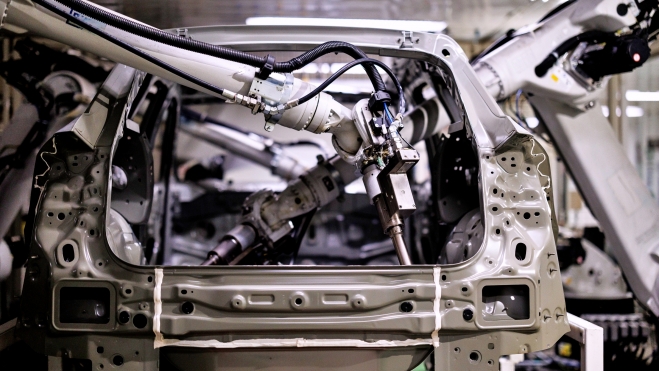
El nuevo Captur está disponible en seis colores, pero también se puede elegir con carrocería bitono, sumando un total de 20 configuraciones diferentes. En Valladolid pueden producir hasta el 80% de su producción con carrocerías bitono. No es cosa baladí, pues cada coche bitono requiere un proceso extra donde varios operarios tienen que cubrir el coche con plásticos antes de pasar por el túnel de pintura otra vez. Dicho de otra manera: un coche bitono se pinta dos veces.
Por su parte, el nuevo Symbioz cuenta con siete posibles colores para la carrocería, entre ellos un nuevo Azul mercurio que supone un desafío extra, pues es una pintura más compleja de crear (los azules, en general, son siempre más complicados).
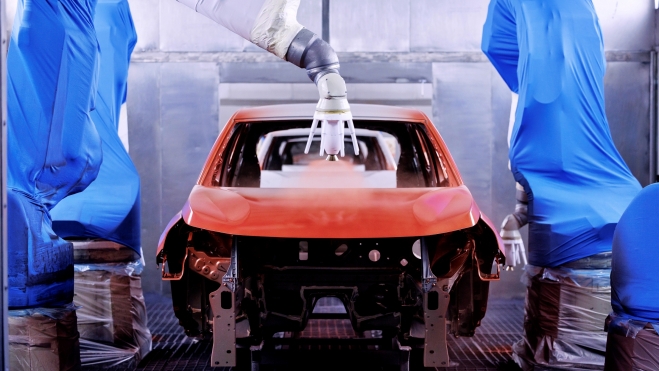
El taller de pintura es capaz de pintar 68 vehículos a la hora y 9 coches seguidos del mismo color. Esto último es importante, pues cuantos más coches seguidos se hagan con el mismo color, menos cambios de pinturas y disolventes hay que hacer en los robots, por tanto se optimiza el tiempo.
El taller de pintura es también uno de los más interesantes desde el punto de vista de la innovación, especialmente enfocada en la reducción de consumos y huella de carbono. Un tema que abordaremos en otro artículo específico, pero que no podemos ignorar aquí. Y es que Valladolid es la única factoría del Grupo que cuenta con el proceso 4wet, lo que reduce a la mitad el número de hornos necesarios para el secado. Por ende, también se reduce drásticamente el consumo de energía.
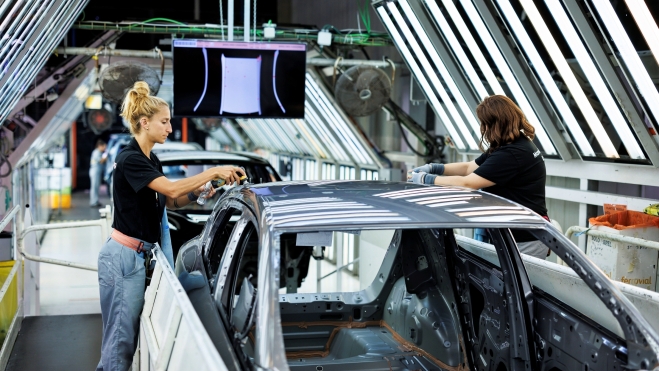
Una vez se terminan los cuatro procesos de pintura (pretratamiento, cataforesis, base de color y barniz), el coche pasa por otro túnel de calidad con una iluminación especial donde los operarios realizan un control exhaustivo de la pintura. Esto se acompaña del "Túnel de detección automática", donde 40 cámaras a lo largo del túnel realizan 65.000 fotos a cada coche (cada cámara realiza 1.625 fotos/minuto) para asegurar la calidad superficial y el aspecto final de la pintura.
Montaje: casi el último paso antes de salir a circular
El proceso de producción termina con el montaje, donde esos conjuntos de acero pintado se convierten en coches funcionales. Esta parte de la línea es donde más personas hay, lógicamente, debido a la complejidad que supone colocar algunas piezas: un total de 1.121 empleados. No obstante, la automatización juega un papel clave, como veremos a continuación.
Las puertas se retiran para mejorar la ergonomía en las operaciones interiores del vehículo. Se colocan en una balancela sincronizada que las transporta paralelamente hasta que se vuelven a montar sobre el mismo vehículo.
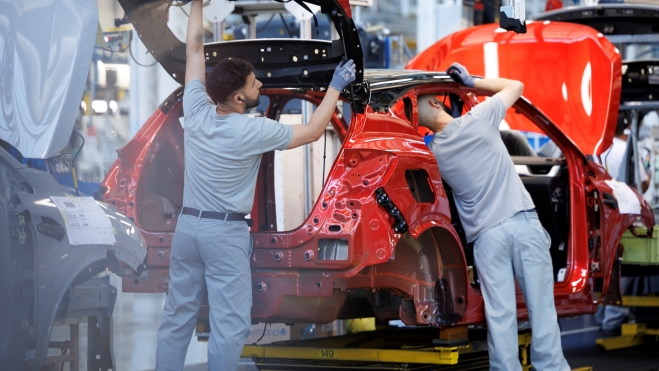
Solamente se necesitan 4 horas desde que llega la carrocería desnuda hasta que se montan todas las referencias, desde el cableado hasta el motor, pasando por el salpicadero, los asientos, ruedas, frenos, sistemas auxiliares, etcétera. Todas las piezas necesarias para cada vehículo han sido preseleccionadas y colocadas en un carro autónomo (AGV) que acompaña al coche en todo el proceso, con una sincronización perfecta entre la línea principal y los AGV. De esta forma, se elimina la elección de piezas en el borde de la cadena, evitando la carga cognitiva de los operarios y reduciendo la posibilidad de errores. En cada carro autónomo van las piezas justas para cada coche; si sobran, alguien debería preocuparse.
El motor y las baterías también salen de Valladolid
Tanto el Captur como el Symbioz se ofrecen con la mecánica híbrida E-Tech de 143 CV, un sistema que ofrece muy buenos consumos. Renault también saca pecho en este apartado, pues casi todo lleva el sello de hecho en España. El motor de gasolina se fabrica en la fábrica de motores de Horse, anexa a las líneas de producción, y el ensamblado de baterías para vehículos híbridos se realiza en el departamento SPB, perteneciente a la Factoría de Carrocerías.
Existen dos talleres: uno para las baterías de vehículos híbridos no enchufables (Captur, Symbioz, Austral, Espace y Rafale) y otro taller para las baterías del Rafale híbrido enchufable. Aquí solamente se ensamblan los módulos, pues las celdas las fabrican proveedores de China.
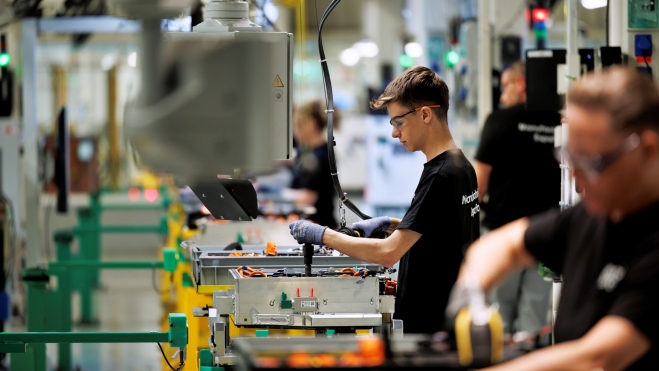
Una vez que se han unido el grupo motopropulsor y la carrocería (lo que algunos fabricantes llaman el matrimonio), el vehículo sigue avanzando por la línea de montaje y se instalan de nuevo las puertas que se retiraron por ergonomía, se montan las ruedas y se añade combustible y otros fluidos necesarios para su funcionamiento. Al final de la línea, el vehículo ya terminado arranca por primera vez. Pero todavía no es el final.
Antes de salir con destino al concesionario, todos los coches se someten a una especie de ITV donde comprueban el ajuste de ruedas, el reglaje del haz de luz de faros, el reglaje de dirección, la calibración y funcionamiento de los ADAS, y se realiza una prueba dinámica en el banco de rodillos donde se acelera hasta 130 km/h y después se frena. Esto sirve para calibrar los calculadores del vehículo. Ahora sí, el coche está listo.
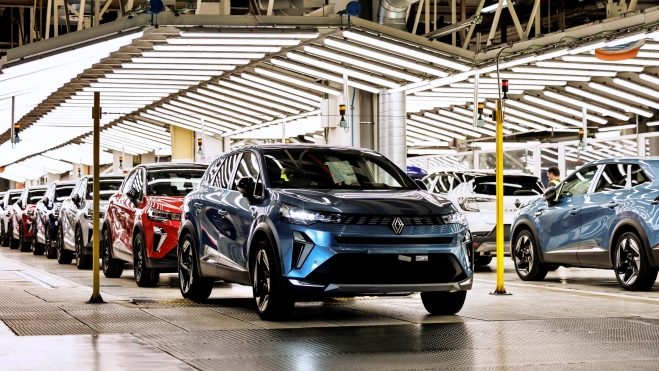
Desde su inauguración, en Valladolid se han fabricado más de 8 millones de Renault. Más de 2 millones han sido Captur (sumando todas sus generaciones) y con el Symbioz quieren seguir la senda del éxito. El año pasado fabricaron 172.733 coches, de los cuales exportaron el 90%, incluidos países con el volante a la derecha como Reino Unido o Australia. Y si no hay sobresaltos, en 2024 superarán los 200.000 coches.