En la mayoría de los casos, los coches eléctricos tienen un precio notablemente más elevado que uno de combustión de similares características. Esta diferencia es todavía mayor en aquellos con una autonomía de 400 kilómetros o más. Estos modelos son, para muchos, completamente inaccesibles, convirtiendo incluso a los vendidos por fabricantes tradicionalmente generalistas en modelos prémium. ¿Es factible poner en el mercado un vehículo eléctrico asequible? ¿Cuáles son los requerimientos para lograrlo?
Hoy en día, la oferta de vehículos asequibles es muy escasa. O bien se trata de coches que ofrecen unas especificaciones y equipamientos mínimos y escuetos, como es el caso del Dacia Spring, o se trata de fabricantes chinos como es el caso de MG. En el futuro, muchos son los fabricantes tradicionales que anuncian modelos pequeños a precios que rondarán los 20.000 €, como es el caso del nuevo Citroën ë-C3.
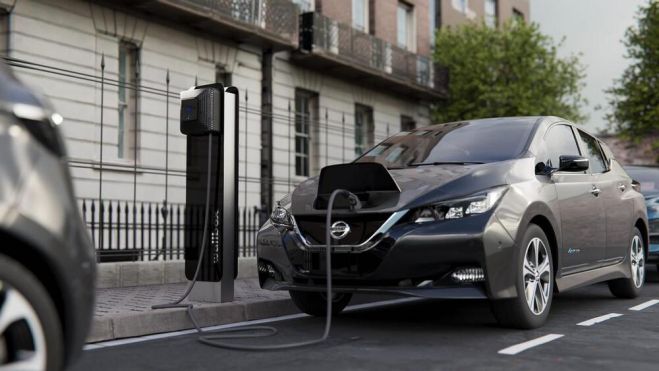
El secreto del coche eléctrico barato desvelado por dos expertos
Para comprender el precio de venta con el que sale al mercado un producto, el primer paso es conocer sus costes de fabricación. Andy Palmer, que ocupó el cargo de director de Operaciones en Nissan, encargado del lanzamiento del Nissan Leaf y responsable directo del área de baterías y vehículos eléctricos de la empresa, se lo ha explicado a Autocar en su podcast My Week In Cars.
“En el momento del lanzamiento, el coste de producción superaba el precio minorista sugerido por el fabricante. Por lo tanto, no solo no estábamos cubriendo nuestros gastos generales, sino que ni siquiera recuperábamos el coste de los materiales". En aquel momento, la estrategia de Nissan de liderar el mercado de vehículos eléctricos perdiendo dinero con cada una de las unidades vendidas “fue una decisión similar a la adoptada por Toyota durante el lanzamiento del primer Prius híbrido”, afirma Palmer.
No obstante, esta comparación es algo arbitraria porque un coche eléctrico cuenta con una batería considerablemente más grande que la de un híbrido. Palmer explica brevemente con algunos cálculos básicos, el coste de la batería: “en aquel entonces, las baterías costaban alrededor de 1.000 dólares por kWh, mientras que en la actualidad su precio es muy inferior, alrededor, de 150 dólares/kWh”.
Partiendo del supuesto de que los fabricantes consideran que la batería media para que un coche eléctrico pueda cumplir con todo tipo de desplazamientos es de 60 kWh, eso implica que el paquete de baterías cuesta 9.000 dólares. Si se le suman los costes generales y el margen de beneficio del suministrador del 15% “el precio final de venta es de 41.500 dólares,” sin considerar ningún beneficio para el fabricante, indica Palmer.
Por otro lado, está convencido de que el precio de la batería continuará disminuyendo, hasta llegar a los 80 dólares por kWh para el caso de una batería de alto rendimiento estándar, aunque esto no suceda hasta dentro de algunos años, ya que el ritmo de reducción de los precios se está desacelerando.
Mientras este momento llega, la otra estrategia para lograr un vehículo eléctrico asequible es reducir el tamaño de la batería. Con una batería de 24 kWh (el tamaño de la del Leaf original) a 150 dólares por kWh, el coste de producción sería de 20.000 dólares para que el fabricante no incurra en pérdidas, calcula Palmer. “La clave para lograr un vehículo eléctrico asequible no es esperar a que la tecnología madure ni necesariamente manipular la química: simplemente implica utilizar una batería de menor tamaño. Para implementar una batería más pequeña, se requiere la infraestructura de carga, y eso es crucial".
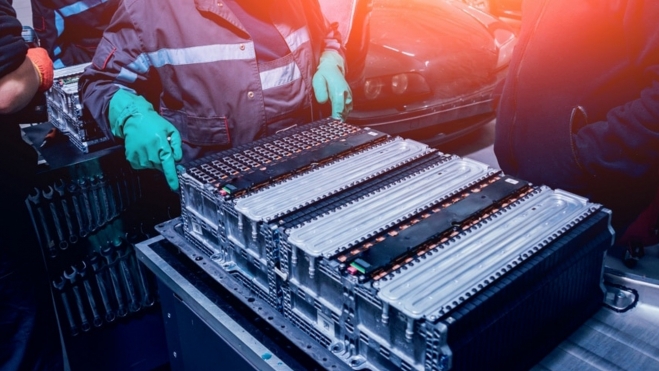
La red de recarga necesaria para reducir la capacidad de las baterías
Palmer calcula que, para una red de carga sólida formada por cargadores rápidos y domésticos, se requieren alrededor de 15 millones de puntos de carga: "a menos que se establezca rápidamente una infraestructura eficiente, es poco probable que el mercado opte de manera natural por un vehículo eléctrico”.
La preocupación por la autonomía continuará siendo un obstáculo y cambiar esa mentalidad resultará complicado. Sin embargo, una red de carga que garantice que siempre habrá acceso a un cargador permitiría reducir el tamaño de la batería: “ese es el momento en que se produce la transformación”.

Más allá del precio de compra
David Greenwood, especialista en sistemas de propulsión avanzados de Warwick Manufacturing Group, explica que el coste de un vehículo eléctrico implica muchos más factores que simplemente el precio de compra. Destaca que "cuando se habla de costes entran en juego no solo el de adquisición sino el de toda la vida útil del vehículo”.
En el caso de los vehículos eléctricos el coste total de propiedad es, posiblemente, una consideración más importante que en el caso de los convencionales. "Para aquellos que adquieren el vehículo eléctrico adecuado (aquellos propietarios que aprovechan al máximo la autonomía que ofrece), el coste total de propiedad juega a su favor", explica.
La clave reside en adquirir un vehículo eléctrico con una capacidad de batería que se adapte a las necesidades. “Si inviertes una gran cantidad de dinero en un automóvil capaz de recorrer 600 km con cada carga y luego solo conduces 15 km cada día, estarás pagando una batería y los sistemas adicionales sin aprovechar al máximo el ahorro de combustible que ello conlleva", aclara. Para un uso urbano, en muchos casos, sería suficiente con un coche eléctrico de 250 km de autonomía.
El modelo chino de crear automóviles pequeños, ligeros y prácticos para uso urbano, que tienen un costo inferior a los 10.000€, “es un concepto que definitivamente vale la pena tener en cuenta en el futuro”.
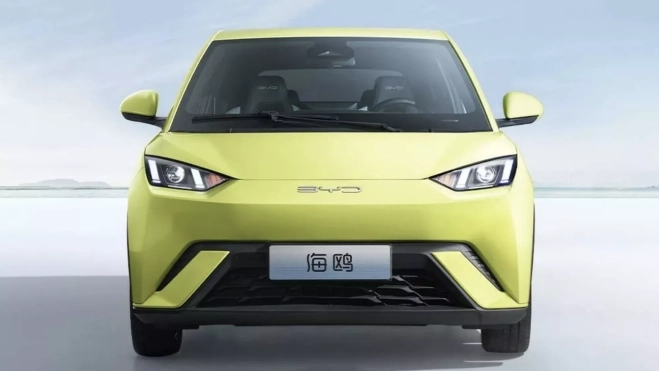
El último eslabón de la cadena
Greenwood añade también la cuestión de que las baterías pueden fabricarse de manera más económica, aunque “ese es el último eslabón de la cadena". Actualmente, las baterías de los vehículos eléctricos se componen de numerosas celdas, reunidas en módulos, que se ensamblan con un diseño de paquete específico para cada vehículo. "Un fabricante podría optar por crear tres diseños de módulos distintos y luego ensamblarlos en ocho diseños de paquete diferentes, con el objetivo de lograr economías de escala a nivel de módulo", explica.
Sin embargo, con el aumento de los volúmenes de producción, la obtención de economías de escala a nivel de módulo se vuelve menos crítica, resultando más rentable diseñar celdas específicas para un automóvil en particular y utilizar el sistema de ensamblaje Cell to pack (CTP) que prescinde de ellos.
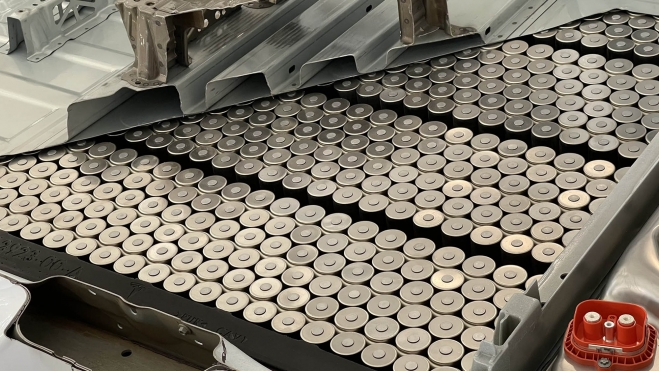
Esta estrategia dará paso a celdas de mayor tamaño, eliminando una capa de los materiales de embalaje, lo que dará como resultado una reducción de costes y también la disminución del tamaño y el peso. La eliminación de una importante cantidad de componentes necesarios para fabricar, ensamblar y gestionar las baterías dará como resultado una reducción de costes potencial que puede ser de hasta el 10% del total.