La autonomía de un vehículo eléctrico está directamente relacionada con la energía que es capaz de suministrar cada una de las celdas que componen su batería. En el caso de las de iones de litio, utilizadas por la práctica totalidad de los modelos eléctricos del mercado, la capacidad energética a nivel de celda y su coste se ven afectados por las características de uno de sus componentes esenciales: el electrodo positivo o cátodo.
Ahora, una investigación del Laboratorio Nacional del Noroeste del Pacífico del Departamento de Energía de Estados Unidos (PNNL), publicado en Energy Storage Materials, resuelve las restricciones impuestas por este electrodo gracias a un novedoso y eficiente sistema de producción de cátodos monocristalinos de alta energía ricos en níquel.

El gran ‘problema’ de las baterías de litio ricas en níquel (NCM)
El cátodo de las celdas de las baterías de los vehículos eléctricos más habitual es ternario o NCM, es decir, está formado por una mezcla de óxidos metálicos, compuesta por óxidos de litio, níquel, cobalto y manganeso (LiNi1/3Co1/3Mn1/3O2). Al incluir una mayor cantidad de níquel en el cátodo, se incrementa significativamente la capacidad de la batería para almacenar energía, es decir, se incrementa la autonomía del vehículo eléctrico en el que se monte.
Las ternas NCM ricas en níquel, como el NCM811 (donde el ‘8’ indica un 80% de níquel), son las que ofrecen un mayor rendimiento en cuanto a alcance. Sin embargo, estos cátodos, creados mediante un método convencional, tienden a agruparse en estructuras policristalinas que presentan una superficie rugosa y grumosa. Esta textura, similar a la de la superficie de una albóndiga, ofrece ventajas para las ternas NCM convencionales, pero no para el caso de las NCM811 y las versiones posteriores.
Las fisuras bulbosas en las estructuras policristalinas son propensas a separarse, ocasionando fallos en el material. Este fenómeno hace que las baterías fabricadas con estos cátodos ricos en níquel sean susceptibles a la formación de grietas, además de iniciar la producción de gases y experimentar una desintegración más rápida en comparación con los cátodos que contienen menor cantidad de níquel.
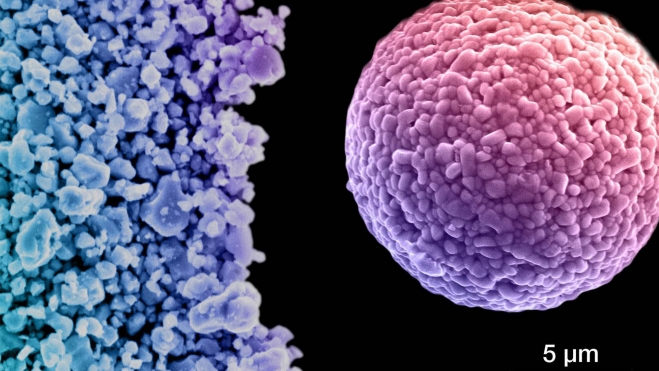
La solución del monocristal NCM811
Una forma de abordar este problema consiste en transformar el NCM policristalino grumoso en una forma monocristalina suave, eliminando así los problemáticos límites entre los cristales. No obstante, decirlo es mucho más fácil que hacerlo. En un entorno de laboratorio, los monocristales se cultivan en diferentes condiciones, como sales fundidas o reacciones hidrotermales, generando superficies cristalinas lisas. No obstante, estos entornos no son prácticos para la producción de cátodos en el mundo real, donde se prefieren métodos de estado sólido más económicos.
Se confecciona un cátodo de NCM combinando un precursor de hidróxido metálico con sal de litio, mezclando y calentando directamente estos hidróxidos para generar el NCM policristalino aglomerado en grupos. Aunque el uso de un proceso de calentamiento en varios pasos produce cristales de tamaño micrométrico, estos aún permanecen aglomerados, lo que perpetúa los efectos secundarios indeseables.
La solución propuesta por la nueva investigación
Bajo la dirección de especialistas en baterías del PNNL y en colaboración con Albemarle Corporation, el equipo de investigación logró superar este problema mediante la implementación de un paso de precalentamiento que modifica la estructura y las propiedades químicas del hidróxido de metal de transición. Al reaccionar el hidróxido de metal de transición precalentado con la sal de litio para formar el cátodo, se genera una estructura NCM monocristalina uniforme que muestra una apariencia suave.
"El proceso de calentamiento de precursores en un solo paso puede parecer simple, pero implica numerosas transiciones de fase a nivel atómico para lograr la segregación monocristalina", señala Yujing Bi, autor principal de la publicación.
Actualmente, los científicos están escalando la producción de monocristales NCM811 a escala de kilogramos, utilizando sal de litio suministrada por Albemarle. Estos monocristales a escala se sometieron a pruebas en celdas de litio tipo bolsa reales de 2 Ah, utilizando un ánodo de grafito estándar, con el fin de garantizar que el rendimiento de la batería estuviera principalmente influenciado por el nuevo cátodo.
“Se trata de un avance importante que permitirá utilizar baterías de litio de mayor densidad de energía sin degradación” asegura Stanley Whittingham, premio Nobel y distinguido profesor de química en la Universidad de Binghamton. "Además, este avance será fundamental para su uso en vehículos eléctricos", añade.
El método de síntesis para el cátodo monocristalino rico en níquel no sólo es tan innovador como rentable, también es fácilmente escalable. Posibilita a los fabricantes de cátodos utilizar las instalaciones de producción ya existentes para fabricar de manera eficiente los NCM811 monocristalinos e, incluso, cátodos con una concentración de níquel superior al 80%.
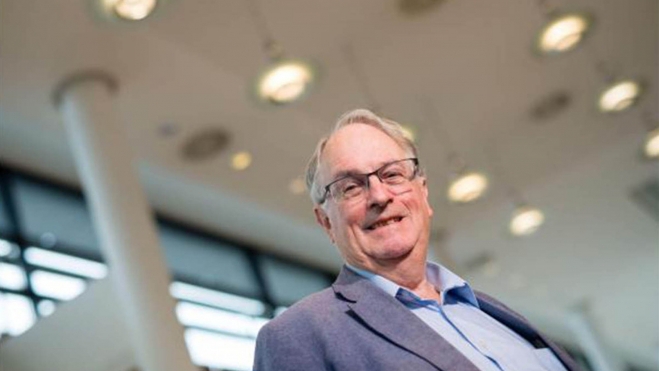
La implementación real de los cátodos monocristalinos
En la etapa de investigación, que se iniciará a principios de 2024, el PNNL, en colaboración con socios de la industria y universidades, llevará la síntesis y pruebas a una escala comercial con el objetivo de avanzar hacia la producción en masa.
Con el fin de lograr este objetivo lo más rápido posible, se emplearán equipos y técnicas de fabricación convencionales que han sido adaptados para incluir la metodología de ampliación desarrollada, junto con algunas otras innovaciones que contribuyen a reducir aún más los costes y la generación de residuos.
"No estamos compitiendo con la industria", afirma Jie Xiao, investigador principal del proyecto y miembro de Battelle en PNNL. “De hecho, nos estamos asociando con líderes industriales como Albemarle para abordar de manera proactiva los desafíos científicos para que la industria pueda ampliar todo el proceso basándose en las experiencias y los conocimientos que hemos adquirido a lo largo del camino".