El incremento en los costes de extracción, procesamiento y transporte de materias primas puede dar como resultado un encarecimiento de las baterías de iones de litio. No obstante, la influencia en el precio final de cada componente de la celda varía, dependiendo de factores como la cantidad utilizada, la demanda y la disponibilidad natural, que impactan de manera dispar en su coste final.
La celda de una batería de iones de litio se compone de un electrodo positivo (el cátodo), un electrodo negativo (el ánodo), un electrolito líquido formado por solventes orgánicos que permite la transferencia de iones de litio entre los electrodos y un separador que evita que las celdas de la batería se cortocircuiten. Según un estudio estadístico de BloombergNEF, el cátodo es el responsable de más del 50% del coste de la batería.
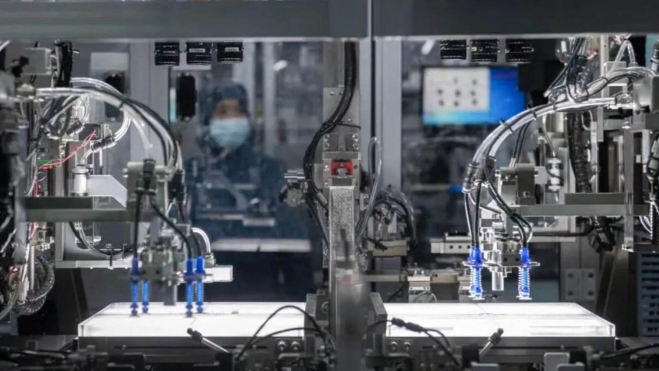
La mejor química NCM, y también la más cara y la menos sostenible
La mayoría de las baterías de los vehículos eléctricos utilizan óxido de litio, níquel, manganeso y cobalto (NMC) mezclados en la estructura cristalina del cátodo. Normalmente, se fabrican disolviendo estos elementos en agua, formando cristales cuando los elementos se unen para formar un sólido. Este proceso requiere grandes cantidades de agua (que luego debe ser tratada para limpiarla) y energía, que son principales responsables del incremento del coste y la huella de carbono.
"La fabricación de los materiales que componen el cátodo de las baterías de iones de litio requiere mucha energía y agua, y produce residuos. Tiene el mayor impacto sobre el medio ambiente, especialmente en la huella de CO2 de la batería", explica en un comunicado el Dr. Mark Obrovac, profesor de Química y Física y Ciencias Atmosféricas de la Universidad de Dalhousie.
En su trabajo de investigación, publicado en dos artículos, en ACS Omega y en el Journal of the Electrochemical Society, Obrovac y su equipo se propusieron explorar la posibilidad de obtener estos materiales utilizando un proceso completamente seco, en lugar de los métodos convencionales que requieren grandes cantidades de agua y energía.
El equipo probó diferentes métodos y condiciones de calentamiento utilizando diversos óxidos para determinar la mejor manera de obtener materiales de cátodo de alta calidad sin utilizar agua y minimizando los desechos. Utilizaron una Fuente de Luz Canadiense (CLS) de la Universidad de Saskatchewan para observar el proceso dentro del horno durante los experimentos, lo que les proporcionó información crucial para mejorar el proceso. Así obtuvieron los mismos resultados, ahorrando energía, agua y dinero.
Los resultados mostraron que, ajustando cuidadosamente los materiales de partida y las condiciones del horno, era posible reproducir materiales de cátodo de tipo NMC con características comparables a los mejores disponibles en el mercado actual. Estos materiales son monocristalinos con partículas de aproximadamente 5 micrones de diámetro, logrando una homogeneidad y calidad óptimas.
Producción a gran escala
Obrovac se ha asociado con la empresa de baterías NOVONIX en Nueva Escocia, que está implementando procesos completamente secos para la producción de materiales de cátodo en una instalación piloto en Dartmouth. Esta planta tiene una capacidad de producción de 10 toneladas por año y utiliza métodos que reducen el coste de producción en un 30%, el coste operativo en un 50% y la energía requerida en un 25% en comparación con los métodos convencionales.
Además, no utiliza agua de proceso y no genera residuos, lo que representa un avance significativo en la producción sostenible de materiales para baterías.